Maintenance management strategies: The 4 main types & when to use them
There are 4 key types of maintenance management strategies including run-to-failure maintenance, preventive maintenance, predictive maintenance, and reliability-centered maintenance.
These maintenance management strategies can be used together, or independently. But, how do you know which strategy will work best for your organisation? And when to use each one?
Breaking it down: types of maintenance management strategies
- Run-to-Failure: This is the simplest maintenance strategy where assets are actually allowed to operate until they break down. The asset receives no maintenance until the failure event occurs and then it’s (hopefully) fixed without causing any production issues. However, when using this method, it’s really critical to have spare parts and reliable staff on hand to replace the failed parts in a timely manner. This strategy is mostly used on assets that don’t have safety risks and have a minimal impact on production.
- Preventive Maintenance (or Preventative Maintenance): This type of proactive maintenance approach includes adjustments, cleaning, lubrication, repairs, and parts replacements. Preventive maintenance software keeps assets in good working order and reduces unscheduled downtime and major repairs.
- Predictive Maintenance: This is a technique that uses condition-monitoring tools to track the performance of equipment during normal operation to detect possible defects and fix them before the asset fails.
- Reliability-Centered Maintenance: This is a strategy that is implemented to optimise the maintenance program of a corporation or a facility. It means having a specific maintenance strategy for each asset that is optimised so that productivity is maintained using cost-effective maintenance techniques.
Now that you have a better understanding of the different types of maintenance management strategies, let’s talk about the pros and cons of each one.
Run-to-failure maintenance
Almost every facilities manager/director uses this simple and credible strategy for non-critical assets, like light bulbs and batteries. There are several reasons why a company would choose to implement this maintenance management strategy.
Pros
- It’s super simple and easy to understand
- There’s minimal planning required
- Fewer people resources are needed since less work is done day-to-date
Cons
- It’s highly unpredictable
- It can be expensive in some cases
- Makes scheduling/planning for staff difficult
- There’s a safety risk involved
To implement a run-to-failure maintenance strategy, you could use paper-based systems or spreadsheets. If you are combining this maintenance management strategy with others, it’s a good idea to use a CMMS so you can track the number of times an asset has been repaired or replaced and all of the costs that go along with it. You can also use a CMMS to track the inventory of spare parts needed to support your run-to-failure maintenance strategy.
Preventive maintenance
Preventive maintenance is probably the most popular maintenance management strategy…at least it gets the most buzz in the industry. When the quality of production is impacted due to unreliable equipment and costs skyrocket because of unplanned servicing, it’s probably time to consider a preventive maintenance program.
Pros
- Minimised asset breakdowns
- Reduced downtime
- Safer work environment
- Increases asset’s productive life
- Improves production quality
Cons
- More labor intensive
- Unnecessary maintenance of equipment (loss of man hours and revenue)
- Doesn’t eliminate catastrophic failures
- Can cause early deterioration of equipment
Even though there are tons of benefits that come along with a preventive maintenance program, the plans can really suffer if there isn’t a reliable way to organise the information. A CMMS or facilities management software can help eliminate the need for stacks of paper and confusing spreadsheets. If used correctly, your team can receive reminders and notifications of upcoming repairs and inspections.
Predictive maintenance
Predictive maintenance is next on the list and can easily be used in conjunction with preventive maintenance. In fact, preventive maintenance usually provides the processes and insights needed to build an efficient predictive maintenance program. This type of maintenance management strategy is mostly used in larger organisations with more complex operations.
Pros
- Decreased maintenance costs
- Reduced unexpected failures and repair time
- Increased production efficiency
- Increased service life of parts
- Improved worker and environmental safety
Cons
- High start-up costs
- Limitations of some equipment
- Misinterpreted data, leading to false maintenance requests
- Difficult to install, configure, and run
When used correctly, the goal of predictive maintenance is to understand the best time to do work on an asset so maintenance frequency is as low as possible and reliability is as high as possible – and avoid all of the unnecessary expenses.
Reliability-centered maintenance
Reliability-centered maintenance (RCM) is a concept of maintenance planning to ensure that systems continue to do what their user requires in their present operating context. Put simply, it’s the process of determining the best effective maintenance strategy for each asset inside your building or facility by combining all of the methods above.
Pros
- Increases equipment availability and reliability
- Reduces maintenance costs
- Lowers staff costs
- Helps to prevent loss of life, property damage, and environmental harm
- Incorporates root cause analysis
Cons
- Really high up-front costs for training and equipment
- Savings potential not evident to management
- To be effective, RCM requires a certain level of maintenance maturity to ensure accurate and complete asset data
Pulling it all together
Above all, your job as the head of facilities is to create a comprehensive maintenance strategy that is efficient, cost effective, and safe. Unfortunately, there isn’t one right answer when it comes to maintenance strategies. You’ll have to come up with the correct blend of strategies that works best for your specific organisation. Planning it all out and making sure to revisit your strategies frequently is the key to success. MRI Net Facilities can help you and your team increase the effectiveness and reliability of your maintenance management strategy. Want to learn more? Schedule a demo here today!
Leading solutions for property occupiers, owners and service providers & contractors.Facilities Management software
Contact MRI Software
Want to find out more about how our innovative software solutions can help your maintenance management strategies? Please click here to schedule a demo, or call us today on .
Voice of the Facility Manager Report – 2025 Australian & New Zealand Edition
The role of the Facilities Manager is ever-evolving. From the adoption of new technologies like AI to the need to adapt practices to suit today’s more flexible building usage requirements, Facilities Managers are being asked to balance numerous respo…
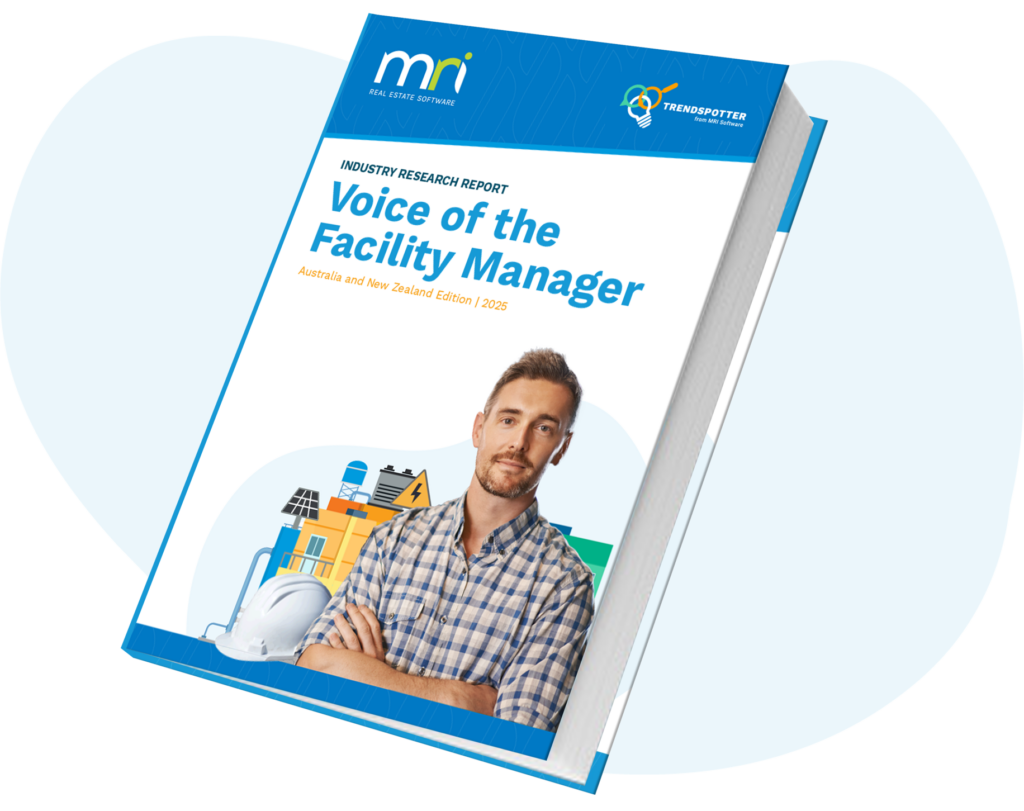